Engineers are looking for a way to continue using Curiosity's drill after a 10-month hiatus, but restoring the drill will probably take several more months.
UPDATE (March 1, 2018): The team has now tested the freehand drilling method at a target called Lake Orcadie. Although the drilling didn't retrieve enough material to collect a sample, the test confirmed that the new method works. Read more in NASA's press release.
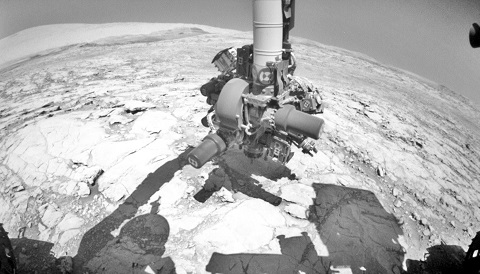
NASA / JPL / Caltech
It's hard to place a repair call when your hardware is on Mars. Never mind the round-trip time delay for communication between the Red Planet and Earth — the difficulty of the call is just part of the lengthy process that occurs when equipment breaks down in the harsh Martian environment.
Now, engineers at NASA's Jet Propulsion Laboratory (JPL), located in Pasadena, California, have announced a possible solution to deal with the balky drill mechanism that has plagued the Mars Science Laboratory (MSL) Curiosity rover since late last year.
A Problem, and a Potential Solution
Curiosity has drilled for samples of Martian rock 15 times since it landed in Gale Crater via a dramatic sky hook landing on August 6, 2012. In the usual drilling scenario, Curiosity places two contact posts on either side of the target rock while the bit is still retracted. Then a motorized feed mechanism, located on the end of the robotic arm, extends the bit forward. The drill relies on the posts for stabilization while the bit's torque and percussive action work its way into the rock, and sensors monitor side-to-side torques on the drill head to avoid having it get stuck in the hole.
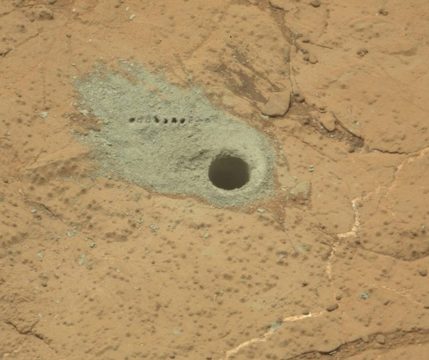
NASA / Caltech / MSSS
Problems began in December 2016, when the feed mechanism failed to extend the drill head. The drilling operations halted at that time, and the cause of the underperforming mechanism remains unknown.
Engineers looked for workarounds for the balky component, and in the end they decided to look for ways to use the drill without using the feed mechanism at all. To do that, they tested alternative drilling methods on a rover replica left here on Earth for exactly this purpose.
One possible solution is to use the robotic arm itself to directly push the drill bit into the rock. That way, the bit can remain extended. Normally, the arm's torque sensor would halt arm motion for the day if it detected an excessive counter force. However, in the new drilling mode, the torque sensor instead helps compensate for side loads, which would normally be taken up by the forward contact posts.
This sort of free-hand drilling is similar to what you might do working on your deck, but it's not easy. "We're replacing the one-axis motion of the feed mechanism with a [robotic] arm that has five degrees of freedom of motion," says Klein. "That's not simple."
JPL engineers have also used the rover replica to work up another way to deliver drilled samples into the laboratory-instrument inlets on Curiosity's deck without using the drill's feed mechanism.

NASA / JPL / MSSS / Emily Lakdawalla.
“We're steadily proceeding with due caution to develop and test ways of using the rover differently from ever before,” says Steve Lee (NASA JPL) in a recent press release. “Curiosity is continuing productive investigations that don't require drilling.”
After extensive testing on its earthbound twin, Curiosity conducted a brief test of the new method on October 17th, touching its exposed drill to the Martian surface for the first time this year. During the test, the drill pushed slightly downward, then sideways, in an effort to measure forces against the arm mechanism.
Onward and Upward
Drill problems haven't prevented Curiosity from doing some good science. Currently nearing the top of the 20-story-tall Vera Rubin Ridge on Mount Sharp, Curiosity examined the distribution of the iron-oxide mineral hematite to confirm that a lake filled the Gale Crater region billions of years ago. The rover has even stumbled across the odd meteorite dotting the Martian landscape.
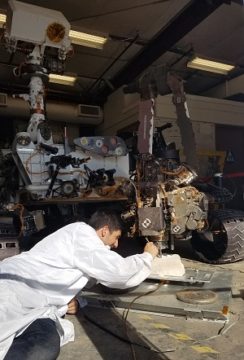
NASA / JPL / Caltech
Although Curiosity was originally slated for a 687-day (669 Martian sols, or one Mars year) primary mission, you can expect NASA to get as much science as possible out of the rover. Thus far, Curiosity has dealt with a stubborn drill, chewed up tires, and a computer memory glitch. But its plutonium-238 power source has an 88-year half life, and that should keep the rover chugging along for decades to come.
And of course, lessons learned from Curiosity will be paid forward to its upgraded twin, the Mars 2020 Rover. Set to launch in July 2020, NASA's next Mars rover will land via a sky crane landing over one of three finalist landing sites.
Watch for drilling operations on the Red Planet to resume in the coming months, with more great science ahead.
Comments
Graham-Wolf
November 1, 2017 at 1:24 am
Good luck Curiosity!
Every time I look up at Mars, I will be thinking of you.
You're quite a star performer.
Graham.W. Wolf at 46 South, Dunedin, NZ.
You must be logged in to post a comment.
Peter Wilson
November 1, 2017 at 2:31 pm
"We're replacing the one-axis motion of the feed mechanism with a [robotic] arm that has give degrees of freedom of motion," says Klein. Give degrees of freedom?
You must be logged in to post a comment.
Monica Young
November 2, 2017 at 9:33 am
That should say "five" - thanks, I'll make the change to the text.
You must be logged in to post a comment.
You must be logged in to post a comment.